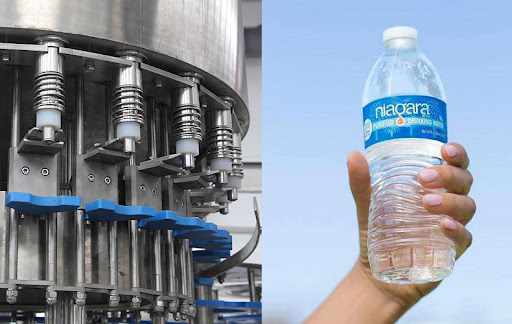
Mineral water production is a meticulous process that requires precision and efficiency. The machinery that ensures the water is purified, bottled, and ready for consumer use is at the heart of this process. Like any sophisticated equipment, mineral water machinery demands regular maintenance to operate optimally. Proper maintenance not only extends the lifespan of the machinery but also ensures consistent production quality, reduces downtime, and minimizes operational costs. In this article, we'll explore essential maintenance tips for mineral water machinery, providing insights to keep your production line running smoothly.
1. Regular Inspection and Monitoring
The first step in maintaining mineral water machinery is regular inspection and monitoring. Routine checks allow operators to identify potential issues before they escalate into costly repairs or significant downtime. Key components to inspect include:
Filtration Systems: Ensure filters are clean and functioning correctly. Clogged filters can lead to contamination and reduced efficiency.
Pumps and Motors: Check for unusual noises, vibrations, or overheating, which could indicate wear or misalignment.
Conveyor Belts: Inspect belts for wear and tear, and ensure they are properly aligned and tensioned.
Sealing and Packaging Units: Look for any signs of malfunction in sealing and packaging units, as these are critical to maintaining the integrity of the bottled water.
A comprehensive inspection schedule should be in place, with logs maintained to track the condition of each component. This proactive approach helps in planning maintenance activities without disrupting production.
2. Adhering to Manufacturer's Guidelines
Each piece of mineral water machinery comes with a manufacturer’s manual that includes specific maintenance guidelines. These guidelines are tailored to the machinery’s design and operational requirements, making them an invaluable resource for maintenance teams. Adhering to these guidelines ensures that maintenance activities are performed correctly and at appropriate intervals.
Key areas where the manufacturer's guidelines should be strictly followed include:
Lubrication Schedules: Different machinery components require lubrication at varying intervals. Over-lubrication or under-lubrication can cause damage, so it’s crucial to follow the recommended schedules.
Replacement Parts: Always use the manufacturer’s recommended parts when replacements are necessary. Non-genuine parts may not meet the required specifications, leading to poor performance or premature failure.
Calibration Procedures: Regular calibration of sensors and control systems is essential to maintain accuracy in production. Follow the manufacturer’s instructions to ensure proper calibration.
3. Implementing a Preventive Maintenance Program
Preventive maintenance is a proactive approach that focuses on regular, planned maintenance activities to prevent unexpected breakdowns. This program involves scheduling maintenance tasks at predetermined intervals based on the machinery’s usage and operating conditions.
Key elements of a preventive maintenance program include:
Routine Cleaning: Regular cleaning of machinery helps prevent the build-up of contaminants that can affect performance. For example, cleaning the nozzles and valves in the bottling section ensures a smooth filling process.
Scheduled Inspections: Inspections should be scheduled based on the manufacturer's recommendations and the machinery’s operational intensity. This could involve daily, weekly, or monthly checks.
Timely Component Replacement: Wear and tear are inevitable in any machinery. Replacing components like seals, gaskets, and bearings before they fail is crucial to avoiding unplanned downtime.
Systematic Testing: Regular testing of machinery performance, such as pressure and flow rate in pumps, ensures that the equipment operates within the desired parameters.
Implementing a preventive maintenance program enhances the machinery's reliability and optimizes production efficiency by minimizing interruptions.
4. Training and Skill Development for Operators
Well-trained operators are essential for the proper maintenance of mineral water machinery. They are the first line of defense in identifying and addressing potential issues. Regular training sessions should be conducted to ensure that operators are familiar with the machinery’s operation and maintenance procedures.
Key areas of training should include:
Basic Troubleshooting: Operators should be able to identify and troubleshoot minor issues, such as adjusting settings or replacing simple components like filters.
Understanding of Machinery Functionality: Operators should understand how each component of the machinery works and its role in the overall production process.
Safety Protocols: Safety is paramount in any production environment. Training should include safety protocols for handling machinery, particularly when performing maintenance tasks.
Continuous skill development ensures that operators can handle machinery efficiently, reducing the likelihood of errors that could lead to equipment damage.
5. Maintaining a Clean and Organized Work Environment
A clean and organized work environment is crucial for effective machinery maintenance. Dust, debris, and moisture can cause significant damage to mineral water machinery if not managed properly. Implementing strict cleanliness standards in the production area can prevent these issues.
Key practices include:
Regular Cleaning: The production area should be cleaned regularly to prevent dust accumulation. Machinery should be wiped down and kept free from debris.
Proper Storage: Tools and spare parts should be stored in designated areas, ensuring they are easily accessible when needed. Proper storage also prevents damage to sensitive components.
Environmental Controls: Ensure that the production environment is controlled for temperature and humidity, as extreme conditions can affect machinery performance.
A well-maintained work environment not only protects machinery but also enhances the efficiency and safety of the production process.
6. Use of Modern Maintenance Tools and Technologies
Leveraging modern tools and technologies can greatly enhance the maintenance of mineral water machinery. These tools provide precise diagnostics and automate certain maintenance tasks, making the process more efficient.
Some useful technologies include:
Predictive Maintenance Tools: Predictive maintenance involves using sensors and software to monitor the condition of machinery in real time. This allows for early detection of potential issues before they lead to breakdowns.
Computerized Maintenance Management Systems (CMMS): CMMS software helps track maintenance schedules, logs, and inventory, ensuring that all tasks are performed on time and that the necessary parts are available.
Automated Lubrication Systems: Automated systems ensure that machinery components are lubricated at the right intervals, reducing the risk of over- or under-lubrication.
By adopting these technologies, companies can improve the accuracy and efficiency of their maintenance programs, ultimately extending the lifespan of their machinery.
7. Documentation and Record Keeping
Maintaining detailed records of all maintenance activities is essential for the effective management of mineral water machinery. Documentation helps in tracking the history of each piece of equipment, identifying recurring issues, and planning future maintenance activities.
Important records to maintain include:
Maintenance Logs: Document all inspections, repairs, and replacements, including the date, time, and personnel involved.
Performance Data: Keep records of machinery performance metrics, such as output rates and energy consumption. This data can be used to identify trends and make informed decisions about maintenance needs.
Parts Inventory: Maintain an inventory of spare parts, ensuring that critical components are always available when needed.
Effective documentation and record-keeping practices enable a more structured approach to maintenance, reducing the likelihood of oversight and ensuring that machinery is kept in optimal condition.
Conclusion
When you start your mineral water business Proper maintenance of mineral water machinery is critical to ensuring the efficiency and reliability of your production line. By implementing regular inspections, adhering to manufacturer guidelines, embracing preventive maintenance, and utilizing modern technologies, you can significantly extend the lifespan of your equipment and maintain consistent production quality. Training operators and maintaining a clean work environment are also key factors in successful maintenance practices. With these tips in place, you can minimize downtime, reduce costs, and ensure that your mineral water production remains competitive in a demanding market.
Write a comment ...