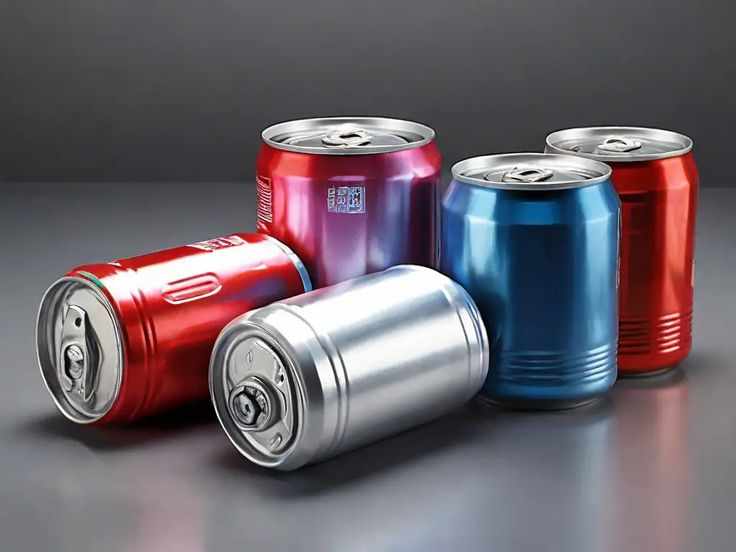
For any soda plant manufacturer, achieving cost-efficiency is vital for profitability and market competitiveness. Whether setting up a carbonated soft drink bottling plant or looking to enhance an existing one, incorporating cost-effective practices can reduce expenses and improve productivity. Below are five essential solutions that can help soda manufacturers optimize their operations while maintaining quality.
1. Automated Production Lines
Investing in automated production lines is one of the most impactful cost-saving measures for a soda plant manufacturer. Automation reduces the need for manual labor, minimizes human error, and significantly speeds up the production process. Automated machinery can handle a variety of tasks, from filling and capping bottles to labeling and packaging, at a consistent and rapid pace. For instance, automatic bottle fillers and cappers ensure precise filling volumes and consistent closure tightness, reducing waste and improving product quality.
While the initial investment in automation might be high, the long-term savings on labor costs and improved efficiency often justify the expense. A carbonated soft drink bottling plant with automated lines can also meet higher production demands without requiring additional staff, resulting in further savings as production scales.
2. Energy-Efficient Equipment
Energy is a significant expense in soda manufacturing, particularly in processes like carbonation, cooling, and heating. Switching to energy-efficient equipment can help cut down on these costs without compromising on productivity. For example, energy-efficient compressors can reduce the power required for carbonation, while energy-saving cooling systems can cut down on refrigeration costs.
Many modern soda plant manufacturers invest in heat recovery systems to make their carbonated soft drink bottling plants even more efficient. These systems capture and repurpose excess heat generated during production, using it to preheat water or other process fluids, ultimately lowering energy consumption. By lowering your energy needs, you can both reduce operational costs and minimize the environmental impact of your soda plant.
3. Bulk Purchasing of Raw Materials
Buying raw materials in bulk is a straightforward yet effective way to reduce costs. Ingredients such as carbon dioxide, water, flavorings, and sweeteners are essential to any soda plant, and purchasing these in large quantities often comes with volume discounts. This can be particularly advantageous for smaller carbonated soft drink bottling plants, where raw materials make up a significant portion of production costs.
Additionally, working with suppliers to negotiate long-term contracts can lock in prices and protect the soda plant from fluctuations in ingredient costs. Planning bulk purchases carefully to avoid waste and storage issues is crucial, but with proper inventory management, bulk purchasing can offer substantial cost savings over time.
4. Effective Water Management Systems
Water is the primary ingredient in soda production, and managing its use efficiently can profoundly impact costs. For a soda plant manufacturer, water is not only a base for the product but also essential in cleaning equipment, cooling systems, and other auxiliary processes. Installing water recycling systems can help reduce overall water usage by capturing and reusing water for non-product applications, such as equipment cleaning.
In addition, employing advanced filtration systems helps maintain the purity of water, which can extend the life of machinery and reduce maintenance costs. Effective water management can also support sustainability goals for a carbonated soft drink bottling plant, enhancing the company’s image while lowering production costs.
5. Preventive Maintenance Practices
Machinery breakdowns and unexpected repairs can disrupt production and lead to significant downtime costs. Adopting a preventive maintenance schedule can help soda plant manufacturers keep their equipment in optimal condition, reducing the risk of unexpected breakdowns. Routine checks on machinery, replacing worn-out parts, and regular cleaning can prevent small issues from developing into costly problems.
Preventive maintenance also extends the lifespan of equipment, allowing soda plant manufacturers to get the most out of their investments. Implementing a computerized maintenance management system (CMMS) can help track maintenance schedules and monitor equipment performance, ensuring that all maintenance activities are handled on time and efficiently.
Conclusion
For a soda plant manufacturer, implementing these cost-effective solutions can improve the efficiency of a carbonated soft drink bottling plant without compromising product quality. From automation and energy-efficient equipment to water management and preventive maintenance, these strategies can help reduce expenses, increase productivity, and improve the plant’s overall profitability. By focusing on smart investments and efficient practices, soda manufacturers can position themselves for long-term success in a competitive market.
Write a comment ...